What is CAD Computer-Aided Design?
Table Of Content
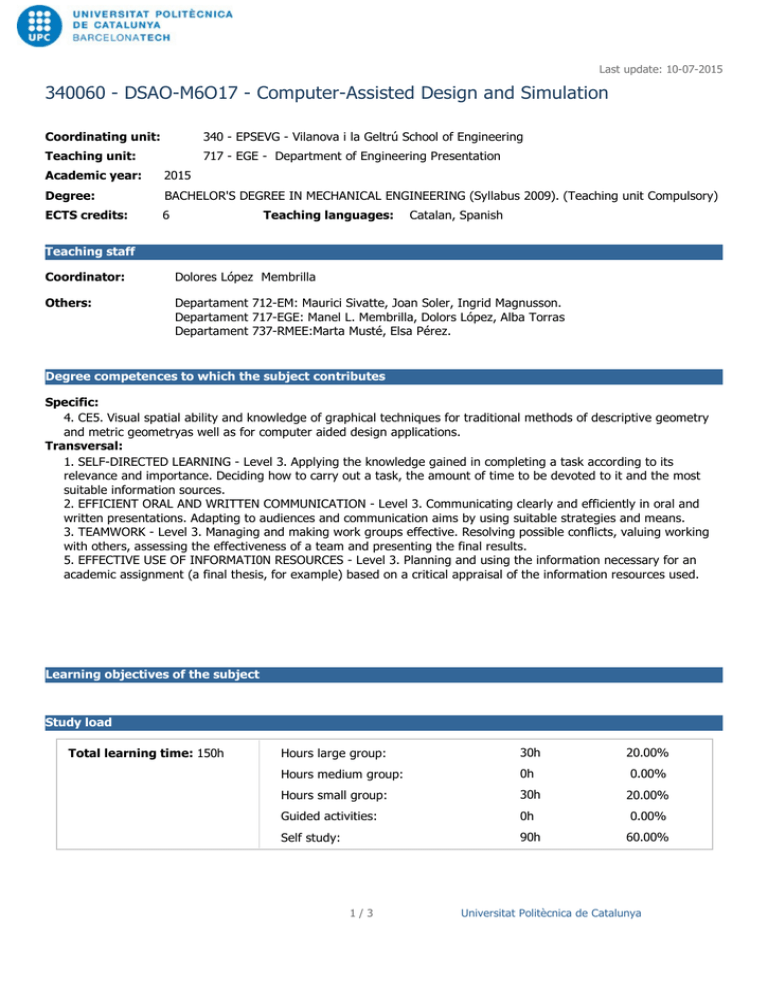
It allows engineers to develop, test, and optimize their design in a safe environment, without having to build expensive prototypes. CAD software also provides a documentation trail, records specifications, and enables collaboration between multiple disciplines and stakeholders in product manufacturing. That is why organizations need to understand how computer-aided design works and its key concepts. Initially conceptualizing their designs, fashion designers employ 2D CAD software programs. CAD is useful in many areas of the fashion design sector, from mass-market to haute couture. At that time, large aerospace, automotive, and other engineering businesses developed internal technologies to automate repetitive drafting tasks.
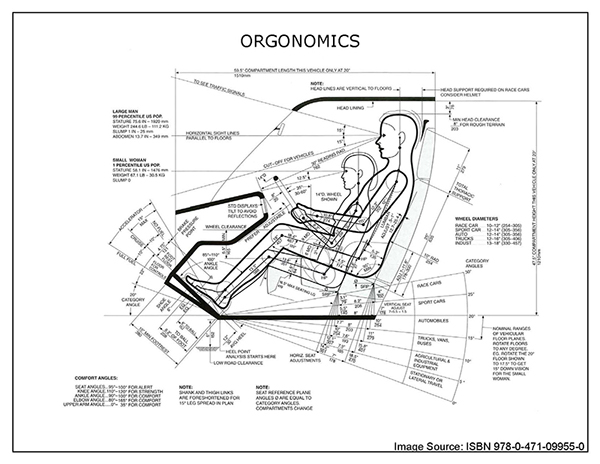
Products and services
CAD software outputs come in the form of electronic files, which are then used accordingly for manufacturing processes. In conclusion, it’s clear that Computer-Aided Design (CAD) has become a cornerstone in various fields, from aerospace and industrial design to the future frontiers of technology integration. Its ability to streamline design workflows, enhance precision, and foster innovation marks it as an irreplaceable tool in modern design and manufacturing processes. CAD (Computer-Aided Design) plays a critical role in aerospace engineering, aiding in the creation of complex aircraft structures, simulating aerodynamics, and optimizing fuel efficiency. CAD solutions have transformed the aerospace industry, enabling engineers and designers to create innovative and efficient solutions.
Coolest 3D Printed Robotics Projects (2024 Update)
Given most CAD software is specialized in a field of design, consider what types of drawings you will make. If you will be designing an HVAC system, look for a program specialized in those types of drawings. Designs can be created and edited in much less time, as well as saved for future use.
Popular CAD software options in construction
Got Digital Gaps in the Manufacturing Enterprise? NIST Engineer Offers Tools to Find Them NIST - NIST
Got Digital Gaps in the Manufacturing Enterprise? NIST Engineer Offers Tools to Find Them NIST.
Posted: Thu, 01 Jun 2023 07:00:00 GMT [source]
Finding the parameter sets that result in a zero first-order derivative and that satisfy the second-order derivative conditions would reveal all local optima. However, in practice, the optimization usually involves multiple objectives and the matters involving derivatives are a lot more complex. It is important to choose the proper CAD software that will fit your company’s product complexity and internal processes. For example, geometry is updated when the numerical value of the dimension is changed in CAD software. The automotive supply chain industry’s major and minor businesses are increasingly using CAD, which is becoming more widely available as their standard software.
For example, Ansys is a popular CAD software used by engineers for finite element analysis (FEA) and computational fluid dynamics (CFD). Blender, on the other hand, is a free and open-source 3D modeling software used in animation, visual effects, and game development. Most credible CAD software producers also offer training tutorials and online courses to go with their products. Nevertheless, the wider CAD community has made support services available and easily accessible through forums, YouTube channels, and dedicated websites.
However, traditional material design methods encounter numerous calculations and experimental trial-and-error processes, leading to increased costs and decreased efficiency in material design. The data-driven model presents an intriguing alternative to traditional material design methods by offering a novel approach to expedite the materials design process. Firstly, a proprietary dataset was constructed for titanium alloy materials using feature design and a combination of unsupervised and supervised feature engineering methods. Secondly, six machine learning algorithms were employed to establish regression models, and the hyperparameters of each algorithm were optimized to improve model performance.
What is CAD (Computer-Aided Design): Your Ultimate Guide
The techniques mostly depend on the shape to be created and the available tools in CAD software. You need to have detailed knowledge of your CAD software tools and processes to know when to use which tool in order to get the desired result. We already discussed in the introduction to engineering drawings that engineering drawing is one of the most represented ways of communicating design intent. In the past, engineering drawings were made with hands, using pen, paper, and different tools for a more efficient drawing process. With the development of computers, the design and drawing practices have been revolutionized. CAD is a tool that every mechanical design engineer should be proficient with, so in this article series, we are going to talk about CAD in great detail to further increase your knowledge in this area.
Explore recently added products
The Best CAD Software in 2024 - All3DP
The Best CAD Software in 2024.
Posted: Tue, 13 Feb 2024 08:00:00 GMT [source]
As its name implies, CAD involves the use of computers to develop, modify, and optimize designs. Today, manufacturers can utilize computer-aided design to create more detailed, accurate, and efficient representations of products. This has led to enhanced quality in manufactured goods and streamlined planning of them. For decades, technology has played a key role in advancing the manufacturing industry. Today’s manufacturing processes are cleaner, more efficient, and more accurate than ever due to the use of automated systems and programming. Computer-aided design (CAD) has a lot to do with manufacturing’s recent evolution—and the exciting job market within it.
Below are a list of three free and three paid CAD training programs that can be found online. Manufacturers save a lot of money and time by making use of features like this one. It enables them to identify flaws in the design of their products before they spend valuable resources to make a prototype. The stress analysis test and other similar applications help the user to modify the design freely until they find a configuration that fulfills the desired performance requirements. All drawings needed to be absolutely accurate as any adjustments would cost too much time and money to incorporate. Today Cylwik regularly uses “a host of different CAD-related tools.” With their help, he can develop accurate models of something yet to be designed.
Parametric modeling tools allow parameters to reference other parameters through relations or equations. The power of this approach is that when one dimension is modified, all linked dimensions are updated according to specified mathematical relations, instead of having to update all related dimensions individually. Furthermore, parameter values are stored in a database (for example, an Excel sheet), and changes made in the database will automatically update the geometry of the object. In addition, different software can have different modules for modeling solid models with a predefined set of features. For example, there can be a solid module, sheet metal module, welding profiles module, plastic parts module, etc. We will focus on three-dimensional modeling (3-D) as a primary modeling approach, and we will use two-dimensional modeling (2-D) in the following step after the 3-D model has been created.
Parametric design is a powerful feature that allows designers to create designs that can be easily modified and adapted for different purposes. By creating a series of parameters that define the design, designers can quickly make changes to the design without having to recreate it from scratch. This feature saves time and allows for greater flexibility in the design process. CAD software enables designers to quickly create digital prototypes, which can be tested and modified easily. The ability to iterate on designs rapidly and efficiently means that designers can experiment with multiple design options without incurring additional costs or delays. Advancements in computing power, along with the development of new technologies such as cloud computing and virtual reality, are continuing to drive the evolution of CAD technology.
Comments
Post a Comment